Exertherm’s CTM technology enables predictive maintenance for electrical assets by continuously monitoring critical electrical joints within LV and MV switchgear. By detecting temperature changes before issues arise, CTM helps increase personnel safety, reduce electrical failures and improve operational efficiency. Trusted across industries, from data centres and energy to logistics and mining.
The World's No.1 24x7 Thermal Monitoring Solution
Discover Thermal Monitoring For A Changing World
Why 24x7 Thermal Condition Monitoring?
24×7 Condition Monitoring will predict 70% more failures in advance than periodic inspections. Therefore, protecting your critical electrical infrastructure from expensive failure, saving costly repairs / downtime, while reducing Opex costs and increasing safety. The acceleration of IIOT means condition monitoring sensors are vital for future proofing your equipment.
A high percentage of existing electrical infrastructure is currently greater than 25 years old
Monitoring critical assets less than 1% of available time via periodic inspection methods leaves a huge reliance on luck
A rise in temperature is the main symptom of a faulty joint or connection
Just one power outage would cost more than installing 24x7 Thermal Monitoring
Condition monitoring enables fault detection & trend analysis of temperature data 24x7 x 365 days
24x7 Thermal Monitoring removes people from risk and increases facility safety
Why Exertherm?
Exertherm® is the global number one provider of 24×7 Thermal Condition Monitoring for electrical infrastructure, successfully installed worldwide by all major OEMs. We deliver complete solutions for LV/MV Switchgear, MCC Drawers, Dry Transformers and more. We’re so proud of our proven reliability we even offer a zero maintenance lifetime guarantee.
World No.1 Thermal Condition Monitoring Solution with Proven Reliability
Zero Maintenance & Lifetime Guarantee on Sensors
Complete Thermal Monitoring Solution for LV/MV Bus, Cable, MCC + TX
Sensors providing accurate data of uniform quality are a key part of the IIOT jigsaw - no sensors = no data
Wireless sensors pose a potential hacking threat to critical infrastructure. Exertherm is hardwired, and thus avoids any potential hacking issues.
Exertherm solutions are accepted & have been successfully installed in major projects globally by all major OEMs.
Frequently asked questions
From the basics to the more advanced, here’s a few questions we get asked a lot. If your question isn’t answered here please contact us at exertherm@kvrel.com
- The most important issue is that wireless sensors create a potential threat to critical infrastructure operations because such systems are hackable. Exertherm sensors avoid any cyber security risks.
- Sensors described as wireless often have a very limited transmission distance – sometimes as low as 30 cm (SAW technology).
- Wireless sensors require antenna to pick up the wireless signal –usually several antennas will be required per vertical column
- The antenna are hard wired !- so perceived savings are actually not available.
- Wireless sensors operate on a limited number of frequencies – which can result in confusion if antenna pick up two sensors on same frequency – causes commissioning problems
- The wireless systems can only normally be commissioned on-site
- Wireless sensors require power to transmit the signal – that creates problems such as battery replacement costs / insufficient power to generate energy harvesting on LV equipment / requirement for re-calibration etc etc.
- Exertherm sensors avoid ALL these issues + Exertherm sensors come with a Lifetime Warranty/ zero maintenance guarantee – something wireless sensors cannot guarantee.
- Raw data can be exported from Exertherm Datacards in Modbus 485 protocol
- Raw data can be exported in Modbus TCP/IP via use of a converter or via the Exertherm ARM XL HMI module
- Local and remote dry contact relays can be utilised via the Exertherm ARM XL module
- The MCC monitoring solution enables remote alarm via dry contact relay / export of raw data via Modbus 485, or export of raw data in Modbus TCP/IP via the Exertherm ARM XL HMI
- The MCC monitoring solution also provides a drawer/ bucket face mounted status LED to indicate Green = OK; Yellow = Warning level alarm; Red = Critical level alarm
LV and MV switchboards –key monitoring points using Exertherm non-contact passive infrared sensors.
- bus joints of line and load side of main incomer air circuit breakers
- line and load side of bus couplers / tie breakers
- Load side of ACB feeders
- optional shipping split bus joints
LV cable terminations;
- Line side main incomer ACB
- Load side feeder ACB
LV MCC : Using the Exertherm MCC kit which provides monitoring of incoming + outgoing power terminations fits INSIDE the drawer/ bucket.
Dry Resin Core Transformers using Exertherm non contact passive infrared sensors:
- Tap change connections
- HV both ends of coil terminations
- LV side bus joints
LV Power transformers :
- Input / output cable terminations
- Tap change connections
Independent research indicates that there will be generic savings of circa 12% on current Opex maintenance costs. In addition, 24×7 condition monitoring will detect approx. 70% more failures in advance of the failure than periodic inspections. This will save on repair and replacement of equipment + associated downtime costs. The combined effect will produce circa 30% overall savings when compared to periodic inspection maintenance regime.
Calculations for typical 10 x switchboards with 5 columns per board indicate total savings of circa $250,000 over lifetime (20yr) of equipment.
There is also the Opportunity cost of not utilising condition monitoring. These include lost opportunity to increase safety by removing people from a place of potential risk to perform inspections.
Perhaps the greatest lost opportunity of not utilising condition monitoring will be the loss of the ability to collect 24×7 data of uniform quality for subsequent analysis to obtain the benefits of IIOT. Every piece of electrical equipment e.g. LV/MV switchboards, MCC, transformers etc which is built without the inclusion of sensors is building in obsolescence.
There are a number of reasons which can be summarised as:
- Thermal inspections on electrical equipment are normally undertaken annually – that is one day out of 365 – less than 1% – which means a high dependence on luck to detect a failure condition in advance of the failure.
- Thermal inspections are not integrated into SCADA / BMS computerised systems and so cannot provide alarm notifications, trending, analysis etc.
- The thermal inspection temperature measurements are highly dependent on the quality of thermal camera and operator, thus data produced is not of a uniform quality. Further, thermal window infrared transmission deteriorates over time, making accurate indications of Go / No Go situations unreliable.
- Exertherm sensor technology provides proven accurate and reliable data of a uniform quality
- The IIOT “revolution” will globally transform the way electrical infrastructure is procured, operated, and maintained across all major industries. Installing sensors to create the data for subsequent analysis is a key part of the IIOT jigsaw since No Sensor = No data!
- ALL major OEMs now advocate the use of thermal condition monitoring over periodic inspection.
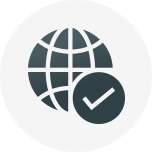
Global OEM Approval
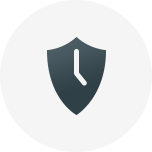
24×7 Thermal Protection
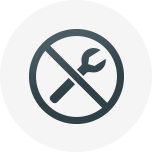
Zero Maintenance
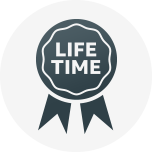
Lifetime Guarantee
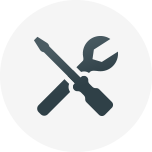
Simple Installation
Solutions
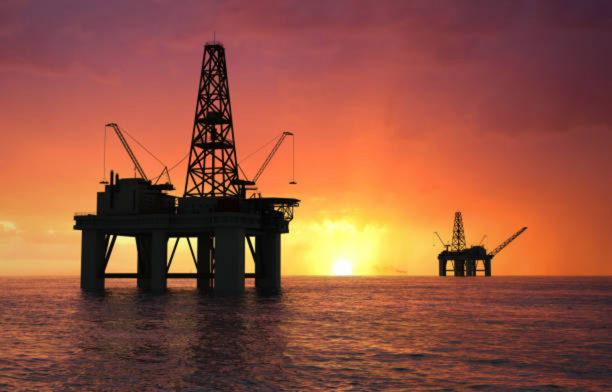
Oil & Gas
Minimize the risk of electrical failures and downtime
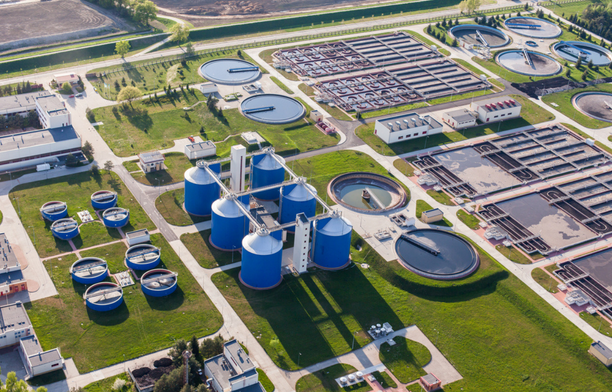
Water and Wastewater
Discover the power to keep pumps flowing 24/7
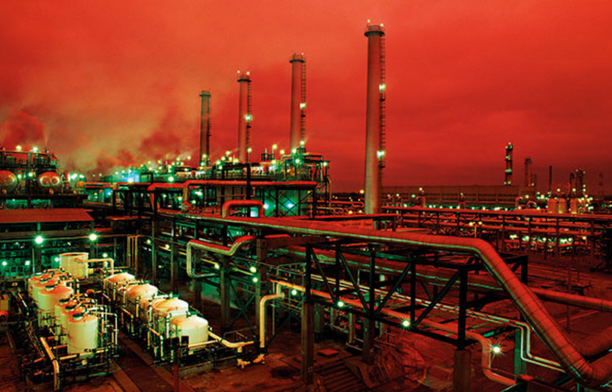
Critical Infrastructure
Ensure your facility stays operational 24/7
Applications
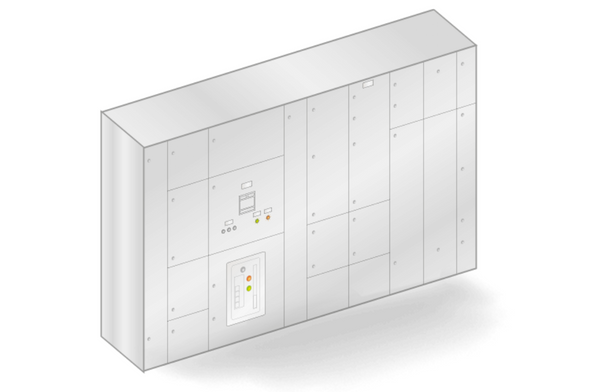
LV Switchgear
Switchgear Temperature Monitoring of critical LV Busbar and Cable Terminations
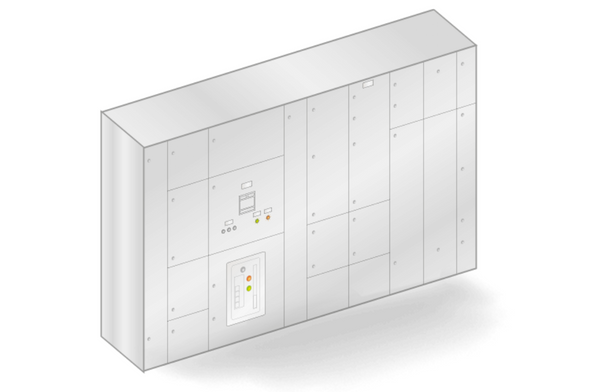
MV Switchgear
Switchgear Temperature Monitoring of critical MV Busbar
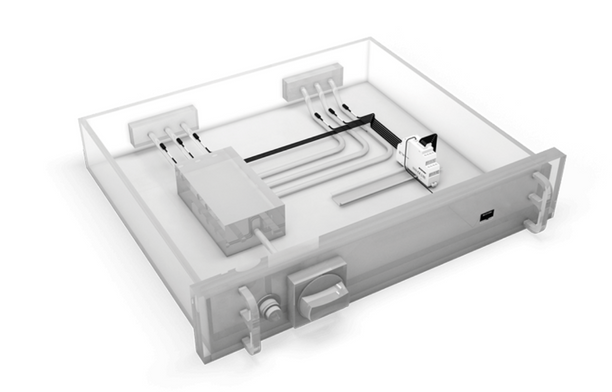
Motor Control Centre
Simple and easy to fit 'in-drawer / bucket' thermal electrical monitoring for MCC
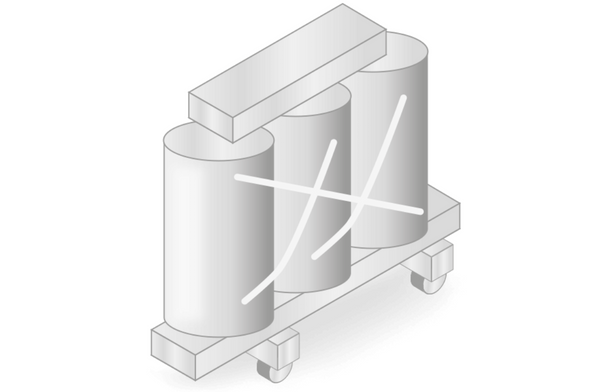
Dry Transformers
Easy, low cost 24x7 Thermal Condition monitoring solutions for common points of failure in Dry Resin Core transformers.
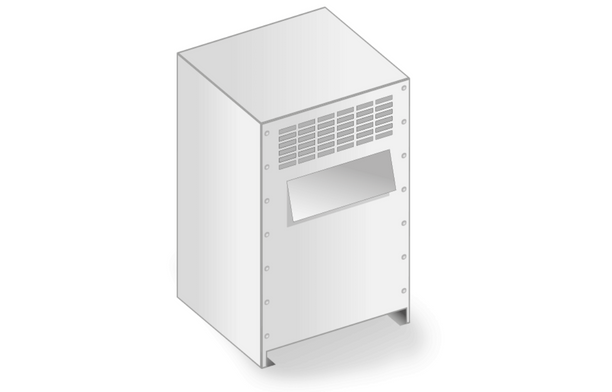
LV Transformers
Cost effective 24x7 Thermal Condition Monitoring solutions for input//output terminations + tap change connections.
Looking for more applications?
Need Thermal Monitoring but can’t find what you’re looking for? We operate in a wide range of sectors from Oil & Gas to Utilities and Marine, so the chances are we cover it! Contact us to find out how Exertherm & KVR Industial can monitor your application.
Email us at exertherm@kvrel.com
Interested? Contact Us To Learn More!
exertherm@kvrel.com
+1 868-293-3547
+1 868-296-7371