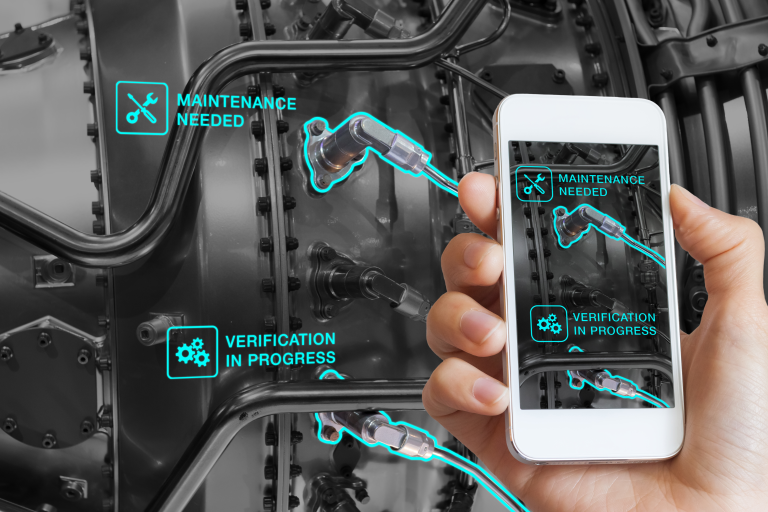
Preventive Vs Predictive Maintenance - the Performance Gap
Rise in temperature as a common cause of power outage
One of the most common causes of power outages and a primary cause of electrical arc flash incidents is the rise in the temperature of a faulty joint or connection. As equipment ages, faulty electrical connections in LV/MV switchgear, and other electrical equipment can increase; studies show that poorly maintained switchgear is 62% more likely to fail.
The accepted ‘best practice’ has, until recently, been a preventive maintenance program in the form of periodic thermal imaging inspections. These are typically annual and often utilizing a combination of an infrared thermal imaging camera and a thermal window. However, although this is an evolutionary step forward from Reactive Maintenance, there remains a very significant ‘Performance Gap’ between the perceived levels of protection compared to the actual level of risk mitigation obtained from a Preventive Maintenance approach.
Predictive Maintenance
Predictive Maintenance (PdM) is the application of proactive and data-driven maintenance techniques intended to assess the state of equipment to determine when repair should be carried out.
To plan corrective maintenance before an electrical asset failure, predictive maintenance software employs data science and predictive analytics to predict potential faults and failures. The objective is to schedule the maintenance when it will be most practical and economical, thus maximizing the equipment lifespan while preventing equipment from being compromised and limiting personnel coming into contact with compromised assets.
The basic structure of a predictive maintenance solution will typically consist of several component parts, including a human interface, a decision support system (or DSS), data collection, storage, and translation, asset health evaluation, prognostics, and condition monitoring.
Preventive Maintenance
Preventive Maintenance (PM) is a form of maintenance that regularly checks equipment and other assets to lower the risk of failure and optimize working conditions.
This proactive maintenance strategy is time-based, also known as strategic maintenance, and includes planned maintenance that could be annually, quarterly, or monthly to streamline planning and implementation. That’s typically organized with the aid of a computerized maintenance management system, also known as CMMS software, to avoid machine downtime and increase assets’ life span.
Running an asset until it breaks down can cost a company up to ten times more in repairs and lost productivity than it would for a company with a planned preventive maintenance policy.
To plan corrective maintenance before an electrical asset failure, predictive maintenance software employs data science and predictive analytics to predict potential faults and failures. The objective is to schedule the maintenance when it will be most practical and economical, thus maximizing the equipment lifespan while preventing equipment from being compromised and limiting personnel coming into contact with compromised assets.
The basic structure of a predictive maintenance solution will typically consist of several component parts, including a human interface, a decision support system (or DSS), data collection, storage, and translation, asset health evaluation, prognostics, and condition monitoring.
Difference between Preventive vs Predictive Maintenance
The difference between preventive and predictive maintenance is that preventive is routine maintenance or inspection, scheduled at regular intervals regardless of equipment condition. This will often incur unnecessary costs, while predictive maintenance is only scheduled as needed based on the asset’s real-time condition. Predictive maintenance, therefore, reduces labor and operational downtime costs whilst increasing safety by removing people from places of risk and increasing the asset’s life.
While factual, the critical issues that create this Performance Gap situation are often not fully explained or understood.
They include:
- Workers remain exposed to risks
- Annual thermography represents an inspection of less than 1% of operational time, leaving 99% dependent on luck
- Timing of inspection often does not reflect the most critical operating electrical loads
- Measurement is reliant on both equipment and operator skills to correlate to the true internal temperature ( thus never be of uniform quality)
- Data remains stand-alone and not integrated rather than dynamically integrated information
- Transmission rates of IR through a thermal window” can deteriorate significantly over time, affecting the accuracy of temperature readings
The manufacturers of thermal imaging cameras state that two requirements are essential to obtain accurate temperature data when conducting a thermal inspection of electrical equipment.
The first is that the camera must have a direct line of sight to the conductor being inspected (thermal windows have variable and deteriorating levels of IR transmission, thus not meeting this requirement).
The second requirement is that the conductor being thermally imaged must operate at a minimum load of 40% of design load. For example, a circuit designed for 3kA must operate at a minimum of 1.5kA during an inspection. This is rarely observed by those carrying out thermal inspections of electrical equipment and is not known by the majority of owners/operators of the equipment.
Maintenance performance gap
Fortunately, there is now a way to close this ‘Performance Gap’ and enhance protection by continuously monitoring and analyzing temperature data, not just identifying but proactively predicting issues arising from faulty connections. Vendor-neutral innovative technology has evolved to provide the ‘next technology step’ of Predictive Maintenance.
With 24×7 thermal monitoring detecting approximately 70% more failure symptoms in advance of failure than periodic inspection. This is achieved via permanently installed temperature sensors, specifically designed for thermal monitoring of electrical switchgear, MCC and transformers.
Thermal sensor technology resolves many of the critical issues identified above and closes the Performance Gap, providing increased safety, more reliable operational uptime, and improving asset integrity.
The accelerating global consumer demand for IOT devices and related products is also fueling the growth of industrial IOT, or IIOT as it is known. This requires industrial equipment and machinery to have embedded condition monitoring sensors, which acquire condition data 24×7, with connection to the internet for subsequent analysis and real-time identification of fault conditions. This enables the most efficient maintenance practice to be adopted, enabling considerable benefits over the life of the equipment, which can be delivered as part of the IIOT / digitization of critical electrical infrastructure. These IIOT benefits include
- Eliminates unnecessary inspection and associated costs
- Reduces intrusive maintenance to ‘as required’ by the condition of the equipment
- Reduces downtime costs associated with periodic inspection/maintenance
- Reduces costs of repairs /replacement parts and associated downtime via increased advance detection of failure symptoms
- Increases safety by removing people from places of risk
- Identifies best performing equipment for future procurement decisions
- Provides OPEX savings from reduced ongoing periodic inspection/maintenance costs.
This accelerating shift from inspection to continuous asset monitoring comes from adopting digitization strategies by virtually every major global company as they strive to remain competitive in the new digital world.
Modernizing electrical infrastructure to include innovative technologies such as 24×7 thermal monitoring will enhance electrical infrastructure’s safety, performance, and life via predictive analytics. No matter what type of electrical installation you are maintaining, a continuous and digital approach to monitoring will provide the most cost-effective and efficient way of ensuring your electrical equipment is protected 24×7, as part of a digitization strategy to remain competitive in the changing digital world.
The COVID-19 pandemic has also led to an increasing recognition that there is now considerable difficulty in sending people to sites to perform time-based preventative inspection or maintenance (often proving to be of little actual value). This put pressure on the personnel performing the inspection, or maintenance, and other site-based staff. The conclusion is that there remains a significant misunderstanding of the perceived level of risk mitigation delivered by preventative inspection/maintenance compared to the actual level delivered.
New sensor technology now resolves this issue and delivers a solution that provides Opex saving and increased safety and avoids building in obsolescence to new build equipment by making it fully compatible with the requirements of digitization. Thus, an essential action for organizations adopting a digitization strategy is to replace thermal windows in electrical switchgear specifications with thermal monitoring sensors, thereby avoiding building in obsolescence to new equipment, which would be a strategic investment mistake.
In addition, when scheduled maintenance shutdowns are planned, this provides the best opportunity to install thermal condition monitoring sensors, thereby upgrading the equipment and making it possible to obtain all the OPEX, safety, and increased uptime benefits, as well as inclusion in IIOT predictive analytics software programs, whilst effectively closing the ‘Performance Gap’ which exists with preventive maintenance.